Water-soluble impregnant improve anti-oxidation property of graphite materials
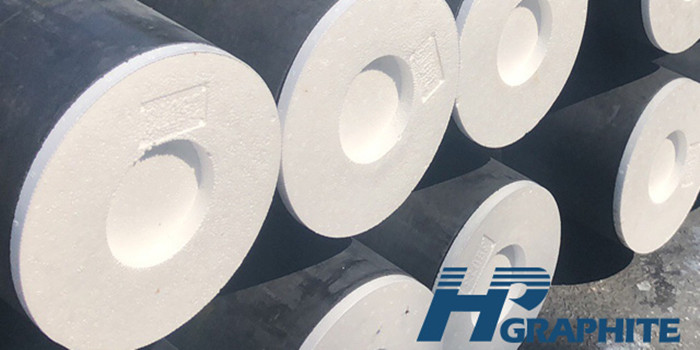
Water-soluble impregnant improve anti-oxidation property of graphite materials
Antioxidant experiment
The oxidation resistance test was carried out in a box-type resistance furnace, and the oxidizing atmosphere was static air. The test temperature is 1,000 ℃. When the furnace temperature reaches the specified temperature, put the sample in the furnace and keep it constant for 2 hours to calculate the oxidation weight loss rate under various immersion conditions. The oxidation weight loss rate calculation formula is: w= (mass before burning - mass after burning) / mass before burning x100%, the dipping condition of the sample with the smallest oxidation weight loss rate is the best dipping condition of the impregnant. The results are shown in Table 2.
It can be seen from Tables 1 and 2: that the sample with vacuum impregnation for 40 min has the lowest oxidation weight loss rate at 1 000 ℃, and the average weight gain rate of the sample under this condition is also the highest. This shows that the antioxidants formed by magnesium dihydrogen phosphate, aluminum dihydrogen phosphate, boric acid, etc. can better fill the pores of graphite materials and cover the active points therein, and exhibit good oxidation resistance at high temperatures. The weight loss rate of the sample immersed in vacuum for 20 min is very small compared with the sample immersed in 40 min. It can be seen that the increase of the anti-oxidation effect by extending the immersion time is very small, so vacuum immersion for 40 min is selected for subsequent experiments as an experimental condition.
Oxidation weight loss of graphite materials under different temperature conditions
Take 2 sets of samples (3 in each group), one of which is immersed in vacuum for 40 min in accordance with the above steps, and the other is not immersed as a blank sample. After the heat treatment is completed, the sample is subjected to an oxidation resistance test at 400~1 000 ℃, and compared with the blank sample. Every 100°C is used as a test temperature point. The sample is kept constant at each test temperature point for 1 hour, then the sample is taken out, cooled to room temperature in air, weighed, and the oxidation weight loss rate is calculated. The relationship curve between oxidation weight loss rate and oxidation temperature is obtained, and the result is shown in Figure 2.
It can be seen from Figure 2 that the graphite sample after impregnation has good oxidation resistance. The unimpregnated sample begins to oxidize at 400°C, and the oxidation weight loss rate increases sharply when the temperature is greater than 700°C. The initial oxidation temperature of samples treated with antioxidants is above 500 ℃. This is because when B2O3 is present in the graphite material, the oxidation reaction activity of graphite can be increased from 194 kJ/mol to 216 kJ/mol, therefore, suppress graphite oxidation; when the temperature is higher than 700 ℃, the oxidation weight loss rate increases more slowly. This is because the phosphate (Al(H2PO4)3, Mg(H2PO4)2, sodium hexametaphosphate, etc.) in the antioxidant impregnating agent loses water and condenses to form polyphosphate at high temperature, coupled with the wetting and covering film-forming effects of the boron-containing substances on the surface of the graphite voids, these substances are thermally stable, so they can reduce the oxidation rate of graphite at high temperatures. And because of the solution impregnation, the antioxidant can well enter the pores of the graphite material to form an anti-oxidation protective layer. This is different from coating antioxidants, which can only play a protective role on the surface of the material, once the surface of the antioxidant layer damage or ablation, the whole material's antioxidant performance will decline sharply.
Conclusion
1) Treating the graphite substrate by the impregnation method can make the graphite material have a good anti-oxidation effect at 700~1 000 ℃. The impregnating agent impregnation conditions were optimized through experiments, and a good impregnation effect was achieved under milder conditions.
2) Since the antioxidants used are all water-soluble substances, the most environmentally friendly water can be used as a solvent to avoid the use of organic solvents, making the dipping operation safer. In addition, an impregnant prepared with an antioxidant that is completely soluble in water can fully infiltrate the finer voids of the graphite material to further improve the impregnation effect. Get more graphite electrodes information.
3) The reason why antioxidants make graphite material anti-oxidation is analyzed theoretically, and the function of each substance in impregnation agent on graphite material anti-oxidation is pointed out, which provides a theoretical basis for searching for better antioxidants.
No related results found
0 Replies