Influence oxidation resistance of graphite--graphitization catalysts experiment
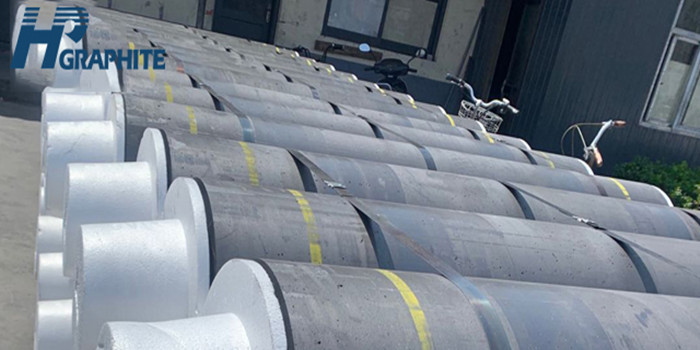
Influence oxidation resistance of graphite--graphitization catalysts experiment
The carbon materials with high graphitization degree were prepared by adding graphitization catalysts. XRD and Raman were used to analyze the structure transformations. The weight loss rate of graphite samples was examined at certain oxidation temperature. Relevant graphite electrodes information. And SEM was used to analyze the microstructure of materials before and after oxidization. The results showed that Pr6O11 could promote the oxidation process, whereas H3BO3 could restrain the oxidation process. Ni2O3 could promote oxidation resistance when the content was low, and had the opposite effect when the content was high.
Graphitization refers to the conversion process of amorphous and disorderly layered carbon material to three-dimensional graphite structure at high heat treatment temperature. Catalytic graphitization is the addition of a certain catalytic substance in the graphite production process to promote carbon products to achieve the required degree of graphitization and other physical and chemical performance indexs at a lower temperature. Catalytic graphitization is an effective way to realize energy saving of graphite chemical process in carbon industry. Scholars from various countries have divided the transition metals in the periodic table into three regions based on the effect of catalysts and carbon: IB-IIB group metals have saturated electrons in the d layer, and their structure is very stable. It is difficult to interact with carbon atoms and does not have a catalytic effect; Group VIII elements, represented by iron, cobalt and nickel, have 6~10 electrons on the d shell, and their electronic energy levels will not change by accepting carbon electrons, so they both can dissolve amorphous carbon to form a solid solution, and cause the catalytic graphite effect of the dissolution and precipitation mechanism; IVB-VIIB elements, represented by titanium and zirconium, have 2 ~ 5 electrons in the d layer of electrons, it is easy to combine with carbon to form a strong covalent bond to form carbides, and the carbides are decomposed into graphite at high temperature, and catalytic graphitization occurs according to the carbide conversion mechanism. In addition, rare earth elements have a very obvious catalytic graphitization effect on various difficult-graphitizable carbons. As a non-metallic element, boron can speed up the uniform and continuous graphitization process of carbon materials.
The oxidation rate of carbon materials mainly depends on the number of surface active sites, the surface area and the impurity atoms contained. Among them, the number of surface active sites is determined by the graphite structure and crystal grain size. The more perfect the crystal structure of graphite, the higher the graphitization degree, the higher the reaction activation energy, and the better the oxidation resistance. Among the carbon graphite materials, the carbon produced by the general binder pitch is preferentially oxidized, so when the oxidation reaction progresses to a certain extent, the aggregate coke particles will fall off. The oxidation reaction mainly occurs on the surface, so the weight loss rate of samples with different surface areas is also different. Some impurity atoms, such as sodium and potassium, play a catalytic role in the graphite oxidation process; other impurity atoms, such as phosphorus and silicon, play an inhibitory role. In this paper, praseodymium oxide, boric acid and nickel oxide are used as additives, and modified pitch and needle coke are used as raw materials to prepare graphite samples to investigate the effect of additives on the oxidation resistance of graphite.
1 Experiment
1.1 Preparation of graphite materials
Mix needle coke, modified pitch and additives in a certain proportion (refer to literature [9] for the particle size ratio and modified pitch content of needle coke) and knead at 155 ℃ for 20 min to form a uniform paste. The paste is placed in a mold at 135 ℃ for preheating for 2 h, and a pressure of 23.6 MPa is used for molding. Then the sample undergoes roasting, two impregnation-carbonization cycles, and finally graphitization at 2 800 ℃. The sample is labeled G-XY (G represents graphite, X represents the abbreviation of additives, and Y represents the amount of additives added).
1.2 Oxidation experiment
Process the graphitized sample into a small square of 20 mm × 20 mm × 10 mm, and weigh the mass m1. Put the porcelain dish in a 800 ℃ muffle furnace and burn it with constant weight; put the porcelain dish containing the sample into the muffle furnace and heat it up to 600 ℃ at a heating rate of 8 ℃/min. After burning for 2 hours, cool down to room temperature with the furnace, and accurately weigh the mass m2. The sample oxidation weight loss rate is
w=(m1-m2)/m1×100% (1)
1.3 Characterization
The crystal structure of graphite is characterized by XRD. The parameters mainly include the apparent crystallite size Lc the interlayer spacing of (002) plane d002 and the graphitization degree g.
The apparent crystallite size Lc is the average stacking height of crystallites in the c-axis direction, which is calculated by Scherrer equation:
In the formula: K is the shape factor, with a value of 0.89; λ is the wavelength of the incident light; β002 is the half-width of the (002) diffraction peak, rad.
The interlayer spacing d002 of the (002) plane is calculated by the Bragg formula according to the angle of the (002) diffraction line.
In the formula, θ is the diffraction angle of the (002) plane.
The graphitization degree g represents the probability of having an ideal lattice structure:
Koeing used Raman spectroscopy to analyze carbon material samples and found that the Raman spectra had two peaks, namely 1 580 cm-1 and 1 360 cm-1. 1 580 cm-1 is the G peak, corresponding to the peak of the graphite structure, and 1 360 cm-1 is the D peak, corresponding to the peak of the defect. Relevant graphite products information. Therefore, I1360/I1580 can be used to characterize the degree of graphitization of carbon materials, namely:
No related results found
0 Replies