Preparation of graphite material with ingredients of secondary powder experiment
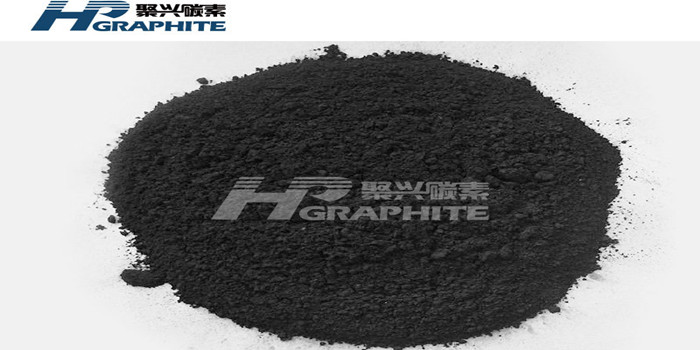
Preparation of graphite material with ingredients of secondary powder experiment
Three kinds of secondary powders were prepared from the calcined pitch coke powder and green petroleum coke powder as the main materials, and modified coal tar pitch and phenolic resin as binders according to certain formula, get the information of graphite electrode products, which were named as the calcined pitch coke-modified coal tar pitch secondary powder, green petroleum coke-modified coal tar pitch secondary powder and green petroleum coke-phenolic resin secondary powder, respectively. The graphite material with high strength and high density from the ingredients of secondary powder was successfully produced by shaping, baking once and graphitizing. The microstructures and morphologies of the obtained products were analyzed by SEM and the thermal analysis of the green petroleum coke-modified coal tar pitch was tested. The results showed that the property of the products exceeded those of the product which was baked tertiary and graphitized. Making use of this formula will shorten production period, reduce production cost and increase economic returns.
High-strength and high-density graphite material is a kind of special graphite material. Generally speaking, the compressive strength of artificial graphite is ≥60 MPa, the flexural strength is ≥25 MPa, and the bulk density is ≥1.70 g/cm3, which can be considered as high-strength and high-density graphite. Because of its high temperature mechanical strength and good oxidation resistance and thermal shock resistance, it has been applied in rocket technology, such as rocket nozzles, combustion chambers, tail rudders, nose cones, etc.; machining molds, EDM, metal continuous casting mold, etc.
Chen Weiran of Hunan University has explored a set of process methods for manufacturing high-strength and high-density graphite: select low-expansion coefficient of petroleum coke and use two-step calcination to ensure its low thermal expansion, and then use particulate dry material to bond with coal pitch, after isostatic pressing and high-pressure baking, as well as high-pressure impregnation and baking, the bulk density of the sample obtained reaches 1.9~2.0g/cm3, and the mechanical strength and thermal conductivity are very good.. Japan's Kureha Chemical Industry Company and Tohoku Kyowa Carbon Company successfully developed ultra-high-density carbon materials in 1978, with a density of 2.0 g/cm3 and a flexural strength reached more than 100 MPa. This method is mainly used for asphalt-based carbon materials. The raw material undergoes a two-step special treatment to improve its graphitization degree, and then it is made by a melt baking and a second baking (graphitization). It does not need to add pitch as a binder. The principle is the same as powder metallurgy, which is directly prepared by melting and sintering raw materials. It has good thermal conductivity, good wear resistance and self-lubricity, strong corrosion resistance, and is easy to be cut.
J.Schmidt, etc. used high-strength and high-density graphite materials to make piston parts on automobile engines. The mesocarbon microspheres with an average particle diameter of 8 μm are selected as raw materials, and they are formed by cold molding at 100 MPa, and then sintered to 1,000 ℃ in a nitrogen environment. Finally, graphite products are obtained through graphitization treatment at 2,500 ℃. The flexural strength reached 102 MPa, the bulk density was 1.93 g/cm3, the thermal conductivity was 105 W/(m·K), and the open porosity was 10%. Yong Gang Wang, etc. used mesophase carbon microspheres as the basic raw material, carbon black is an additive. After a specific process, the prepared carbon material has a compressive strength of 420 MPa and a bulk density of 1.71 g/cm3. Through comparative experiments, it is also concluded that as the amount of carbon black increases within a certain range, the strength and bulk density of the carbon materials also increase.
In this paper, secondary powder is prepared through a specific process route, and then formulated into secondary powder ingredients through a certain formula, and high-strength and high-density graphite materials are prepared through molding, baking, graphitization and other processes.
1 Experiment
1.1 Raw materials and performance
The experiment mainly used calcined pitch coke fine powder (D50 below 19 μm), raw petroleum coke fine powder (D50 below 15 μm), and the binders were modified coal tar pitch and phenolic resin. The properties are shown in Table 1, Table 2 and table 3.
1.2 Process flow
The technological process of the secondary powder is shown in Figure 1.
In the process of preparing the secondary powder, the calcined pitch coke fine powder and the modified asphalt binder are mixed and kneaded according to a certain ratio, and then after rolling and secondary grinding, the secondary powder fine powder is obtained (-200 mesh fine powder purity 95%~99%). When preparing the secondary powder with phenolic resin as the binder, first dissolve the solid phenolic resin completely with alcohol, then mix it with the raw materials, after mixing, drying and grinding into secondary powder fine powder (-200 mesh fine powder purity 93%~97%).
Figure 2 shows the process route for preparing high-strength and high-density graphite materials with secondary powder ingredients.
1.3 Selection of formula and process parameters
In this experiment, calcined pitch coke-modified coal tar pitch secondary powder, raw petroleum coke-modified coal tar pitch secondary powder, and raw petroleum coke-phenolic resin secondary powder were prepared according to a certain formula, and then the secondary powder ingredients of calcined pitch coke-modified coal tar pitch and raw petroleum coke-modified coal tar pitch are prepared through a specific ratio. The number is formula group A, and the second powder ingredients of calcined bitumen coke-modified coal tar pitch and raw petroleum coke-phenolic resin are numbered as formula group B. The formula group A and formula group B are shown in Table 4.
The experiment was molded by a 6.3 MN press. The size of the pressed test product was 310 mm×210 mm×120 mm, the pressure was maintained at 100 MPa, and the pressure holding time was 1 min; visit us for more technological information. and then high-strength and high-density graphite materials were prepared by first baking and graphitization.
No related results found
0 Replies