Preparation of graphite material with ingredients of secondary powder result and conclusion
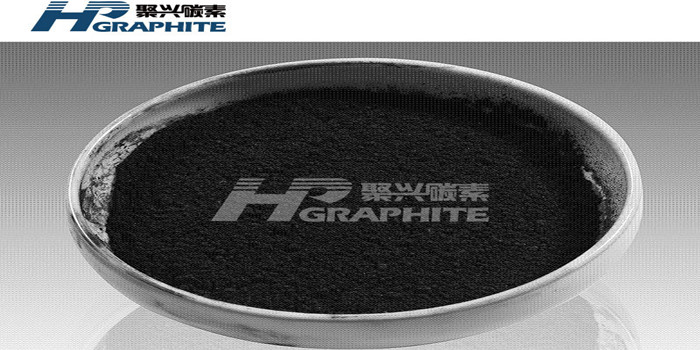
Preparation of graphite material with ingredients of secondary powder result and conclusion
Results detection and analysis
After the samples were baked, the surface of each sample of formula group A was smooth and crack-free, and the sound was loud after being hit with a hammer. To get the information of high quality graphite electrode products. Some samples of formula group B have elongated cracks, some have protruding and deformed surfaces, and some have dull sound after being hit with a hammer, and internal cracks in the product. These phenomena may be related to the low degree of coking of the phenolic resin. The phenolic resin combines better with the raw petroleum coke before baking, but the phenolic resin will coke during baking, and a large amount of organic components will volatilize, so the part combined with raw petroleum coke will form a gap, but also produce internal stress, resulting in cracking of the product.
The baking results show that the secondary powder ingredients prepared by calcined pitch coke-modified coal tar pitch secondary powder and raw petroleum coke-modified coal tar pitch secondary powder are suitable for preparing special graphite materials with high strength and high density fine structure. This article focuses on the performance of each product in formula group A.
1. Performance test of samples
1.1 bulk density
Table 5 shows the bulk density of each sample of formula group A after compression molding, first baking and graphitization.
After the secondary powder ingredients are molded and formed, the bulk density of each green body is above 1.25 g/cm3. After first baking, the bulk density of each sample of formula group A is 1.57~1.65 g/cm3, after first baking, the average increase in bulk density is about 0.35 g/cm3. The bulk density of the green body after a firing is larger than that of the conventional product. This is because the raw material prepared by the green body in this experiment contains green petroleum coke, which has a high volatile content and has self-sintering performance during baking, which results that the volume shrinkage of the baked product is large, and the increase in bulk density is larger than that of conventional products. In this experiment, after first baking, the volume shrinkage rate reached more than 33%, and the product length, width, and height shrinkage rates were all above 11%.
After first calcination, the experimental products were directly graphitized without impregnation and second calcination. After graphitization, the bulk density of these five groups of samples was further increased, and all reached more than 1.70 g/cm3.
1.2 Strength
Figure 3 shows the compressive strength and flexural strength of the five samples of formula group A after a baking and graphitization. It can be seen from Figure 3 that the compressive strength of these 5 samples is between 82~90 MPa, and the flexural strength is between 38~47 MPa. Among them, the compressive strength of the A-2 sample is 90 MPa, and the flexural strength is 47 MPa, which is the best overall mechanical performance among these five groups. The changing laws of these two sets of graphs are also consistent. As the content of raw petroleum coke-modified coal tar pitch secondary powder increases to 40%, the compressive strength and flexural strength of the product reach the maximum, and then as its content increases, the compressive strength and flexural strength of the product gradually reduce. It can be concluded from the law of strength change that the calcined pitch coke-modified coal tar pitch secondary powder acts as a matrix skeleton, while the raw petroleum coke-modified coal tar pitch secondary powder is the reinforcement. When the mass ratio is 60:40, the strength of the prepared sample is the best.
1.3 Resistivity
Figure 4 shows the resistivity of five samples in formula group A after first baking and graphitization.
1.4 Shore hardness
The hardness of carbon graphite materials is generally lower than that of metal materials, and Shore hardness is generally used in the carbon industry. Shore hardness mainly uses the elastic callback method to measure hardness, will not damage the sample. In this experiment, HS-19A Shore hardness tester was used to measure the hardness, and the Shore hardness of the five samples in formula group A after first baking-graphitization was measured, as shown in Fig. 5.
The Shore hardness of sample A in formula group had little difference, and the maximum hardness was A-2 sample, whose value was 47. The smallest sample is A-5, which has a hardness of 38.
2. Comparison of product performance
From the main performance test and comparison of formula group A sample, we can get: the A-2 sample has the best comprehensive properties in each formula group after first calcination and graphitization. The compressive strength of A-2 sample is 90 MPa, the flexural strength is 47 MPa, the bulk density is 1.79 g/cm3, the resistivity is 12.1 μΩ·m, and the Shore hardness is 49. In this experiment, the performance of A-2 sample was compared with that of the company's products of the same specification (310 mm×210 mm× 120 mm), as shown in Table 6.
From Table 6, it can be seen that the A-2 sample after first baking exceeds the level of the company's tertiary baking products in all aspects, but the resistivity is higher, which is related to the fact that it has only been roasted once. By comparing may have to file A, if use A - 2 formula in the production of green after first baking and without dipping, again after graphitization of first baking graphite material can replace conventional three time melting products of the company, so that we can shorten the production period of at least two months, for the company to save the production cost, so as to bring huge economic benefits.
3. Scanning atlas analysis of A-2 sample
The scanning electron microscopy (SEM) images of the A-2 formula sample after first calcination and graphitization are shown in Figure 6. As can be seen from the figure, the inner part of the sample is relatively dense, without obvious cracks and pores, the two kinds of secondary powder after baking and graphitization become graphite phase and well fused together, so that the bulk density of the product is large, and the mechanical strength is high.
4. Thermal analysis of raw petroleum coke-modified coal tar pitch secondary powder
Take the raw petroleum coke-modified coal tar pitch secondary powder for thermal analysis (Figure 7). From the DSC-TG curve analysis, the secondary powder is very stable before 400 ℃, almost no decomposition and polymerization reaction occurs, and there is little quality loss, but there is a huge exothermic peak between 400~760 ℃, which indicates that violent decomposition and polycondensation reaction has occurred, reaching the apex of the exothermic peak at 700 ℃, the reaction is the most violent, the volatile matter of the secondary powder A large amount of reaction is lost, and the mass loss is at least 85% and is accompanied by volume shrinkage. From the thermal analysis of the raw materials, it can be concluded that the volume of the product will shrink as the baking temperature changes during the baking of the green body. After first baking, the bulk density of the product will be greatly improved.
5. Conclusion
Using calcined pitch coke fine powder and raw petroleum coke fine powder as raw materials, modified coal tar pitch and phenolic resin as binders to prepare different secondary powder ingredients, high-strength and high-density graphite is prepared through compression molding, first baking, and graphitization material. The bulk density, strength, hardness and resistivity all meet the requirements of high-strength and high-density special graphite materials; A-2 sample has a compressive strength of 90 MPa, a flexural strength of 47 MPa, a bulk density of 1.79 g/cm3, and a resistivity of 12.1 μΩ·m, Shore hardness is 49, and the performance of the sample has met the requirements for the use of EDM graphite, continuous casting graphite, and sintered mold graphite.
In this paper, a high-strength and high-density graphite material is prepared through first baking and graphitization, which reduces the secondary impregnation and secondary baking compared with the products of the same performance produced by the current enterprise, which can shorten the production cycle and reduce the production cost for the enterprise to get more related technical news contact us.
No related results found
0 Replies