Technology|Graphite products graphitization crack reason analysis Ⅰ
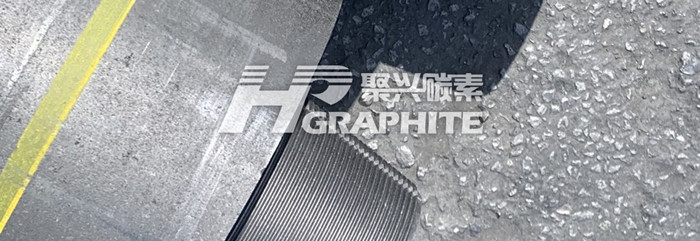
Technology|Graphite products graphitization crack reason analysis Ⅰ
Graphitization is one of the main heat treatment processes in the production process of carbon - graphite products. Acheson graphitization furnace is the main graphitized carbon - graphite products production type furnace at present. It is a special resistance furnace with direct heating and intermittent operation by using the products and resistance materials loaded into the furnace as "internal heat source". The space filled with products and resistance materials in the graphitization furnace is called the furnace core. The cross-sectional area of the furnace core is usually 3-6m2, which supplies a strong current to the graphitization furnace. With the help of the resistance of the graphitization furnace core, the electric energy is transformed into heat energy to make the products reach the maximum temperature of graphitization and complete the graphitization process. It follows Joule-Lenz law.
It can be seen that the temperature at different points in the graphitization furnace core is different, and at the same point, the temperature is also different due to different time. It can be seen that the temperature of the graphitization furnace core is not only a function of space, but also a function of time, so the temperature distribution in each part of the furnace core is uneven.
After the graphitization furnace is powered on, the products are heated by the heat generated by the resistance material, so that the temperature of the furnace core gradually increases. The temperature rise of the furnace core is very uneven, and the temperature distribution is very different. The temperature difference between the center of the graphitization furnace core and the insulation material on both sides of the furnace core can be hundreds of degrees Celsius, and the temperature difference between the upper and lower parts of the furnace core can also be hundreds of degrees Celsius. Therefore, the uneven distribution of heating temperature in the same graphitization furnace core is the main reason for the cracks of furnace core products.
Based on many years of graphitization production experience, this paper briefly summarizes and analyzes the causes of crack waste products in the graphitization production process of carbon graphite products; Here, we will discuss with carbon engineering technicians in order to reduce the crack waste in the process of graphitization production process of carbon - graphite products, improve the yield of graphite chemical sequence, reduce the production cost of graphite chemical sequence, improve the purpose of economic benefit.
Reason of graphitization crack
In the process of graphitization, the internal factor causing cracks is that the quality of the body of the product is not high and the heat resistance is poor. The external factor is that the core temperature rises too fast during the graphitization process, the temperature difference between the upper and the lower parts or around the parts increases, and the thermal stress increases accordingly, which is the main reason for the crack of the product.
1. Graphitization process system is unreasonable
Furnace charging way
Acheson graphitization furnace products are usually installed by the vertical installation method, which has two forms: formal loading and wrong loading. When core products are installed, there is only one high-density current heating belt for any product. The wider the heating belt, the more uniform the heating of the products. On the contrary, the heating is very uneven. In case of wrong installation, there are two high-density current heating belts for each product, and the heating of the product is more uniform than that of the formal installation. Therefore, the charging mode of graphitization furnace products is improperly selected. In the process of graphitization power transmission, the temperature rise speed around the products varies greatly, and the thermal stress generated by the products exceeds the thermal stress that the body can bear, which is very easy to crack the products.
Unreasonable power on system
Acheson graphitization furnace core temperature variation curve is rated power distribution of the power curve is used to control, if the graphitizing furnace electricity system is unreasonable, determine the graphitizing furnace electricity curve starting power is too large and rising power too fast, make the products in the process of electricity, both inside and outside temperature gradient is too large, resulting in thermal stress greatly exceeding the resistance of products and cracks. Especially when the furnace temperature is 1300-1800 ℃, in order to strictly control the rising stage of furnace temperature, the physical structure and chemical composition of products begin to change greatly at this stage, and the graphitization of amorphous carbon does not begin. In fact, it is mainly chemical reaction, and the elements such as hydrogen, oxygen, nitrogen and sulfur combined in the microcrystalline structure of amorphous carbon continue to escape. As a result, the impurity elements at the edge of amorphous carbon microcrystalline structure are continuously reduced, and some lattice defects remain. At the same time, the thermal stress is relatively concentrated, which is very easy to cause cracks in the product.
Resistance of resistance material
Graphitization furnace core resistance is composed of the resistance of the product and the resistance of the resistance material in series. When the graphitization furnace is powered on, the resistance of the resistance material accounts for about 99% of the furnace core resistance, and after the power on, the resistance of the resistance material accounts for about 97%. It can be seen that in the whole graphitization process, the current mainly heats the products through the heat generated by the resistance material. When the resistance of the resistance material is quite different from that of the product, the heat generated by the resistance material is far greater than that of the product itself in the process of graphitization and power on, resulting in too large difference in temperature inside and outside the product, which will cause the thermal stress to crack the product.
2. Graphitization operation quality is not high
The charging quality is not high
Graphitization charging operation does not meet the requirements of process and technical standards. During charging, the furnace core products are arranged irregularly, the product group spacing is inconsistent, the resistance material is filled unevenly, and even the "swelling" phenomenon of resistance material occurs. In this way, the current distribution around the furnace core is very uneven during the power transmission of graphitization furnace, resulting in uneven heating and temperature rise speed of products. The temperature difference inside the product is too large. The resulting thermal stress causes the product to crack and reject.
Resistance material quality is not uniform
When mixed coke is used as resistance material in graphitized charging furnace, because the resistivity of metallurgical coke is 5-8 times higher than that of graphitized coke, if the mixture of metallurgical coke and graphitized coke is uneven, the resistance distribution around the furnace core is very uneven, resulting in uneven temperature rise speed at all parts of the furnace core during power on, excessive temperature difference between the upper, lower and surrounding products, and increased thermal stress, It is easy to produce a large number of crack waste products.
Graphitization furnace core deflection
According to the electric heating law of Acheson graphitization furnace, the temperature distribution in the graphitization furnace core is closely related not only to the resistance of the furnace core, but also to the current passing through the furnace core. When the bias current occurs in the core of Acheson graphitization furnace due to various reasons, the current passing through the core is very different, and the distribution of core temperature is very different. When the current distribution of the furnace core varies greatly, the part with large current generates more heat, the temperature rise of the products in this area is faster, the part with small current generates less heat, and the temperature rise of the products in this area is slower. Therefore, the temperature distribution of the furnace core varies greatly, resulting in large internal temperature difference and corresponding increase of thermal stress, make the waste products.
3. Quality of baked product
Internal crack of baked product
According to the data, the temperature range of 350-500 ℃ and 700 ℃ and above in the baking process of products is the most dangerous temperature range in which carbon materials may be damaged. When the outer surface temperature of the product is 800 degrees and the maximum radial temperature difference is 10.7 degrees, the area with a radius of 50-65mm determines the strength of the material, forming a dangerous tensile stress area within the 65mm radius of the blank center. When the temperature is 700 degrees or higher, the stress in this area is far greater than the limit of the breaking strength of the material, which is the reason for the longitudinal straight crack of the product. Generally, this crack will not extend to the outer surface of the product, that is, the internal crack of the product.
Homogeneity of products
The uniformity of density distribution of carbon - graphite products and the uniformity of radial and axial density distribution of products are closely related to the quality of products during graphitization heat treatment. Where the density distribution of the product is uneven, during the graphitization heat treatment process, due to the action of thermal stress, the product is easy to produce internal stress, and accordingly, the distribution of internal stress of the product is also uneven. This uneven internal stress is easy to cause cracks in the product, resulting in crack waste products in the graphitization process.
The bulk density of the product is high
The bulk density of carbon graphite products mainly changes with the different production raw materials and technological conditions. The flexural strength, elastic modulus and thermal conductivity of products increase with the increase of bulk density. When the volume density is high, the elastic modulus and brittleness of the product increase, leading to poor thermal impact resistance of the product. In the graphitization heat treatment process, the thermal stress caused by high temperature greatly exceeds the stress that the product itself can bear, and the internal and external stresses differ greatly, resulting in crack waste products.
The pre-production process is unstable
As graphitization is the last heat treatment process in the production of carbon - graphite products, it is also the heat treatment process with the highest temperature. It is generally believed that when the production of the current process is unstable or the quality fluctuates, it will be intensively exposed in the graphitization process. If the calcination material temperature is low, the softening point of asphalt is not qualified, the baking temperature is low, and the impregnation weight gain rate is unqualified, the products will cause secondary shrinkage or uneven shrinkage during graphitization high temperature treatment, which is very easy to produce crack waste products.
Inflation phenomenon
Some degree of irreversible volume expansion occurs in the graphitization process of products, which is mainly caused by the rapid escape of sulfur concentration in the graphitization process. The degree of irreversible expansion increases with the increase of sulfur content and the acceleration of heat treatment speed. This irreversible expansion behavior is called "gas expansion phenomenon".
As we all know, the content of non-carbon elements such as hydrogen, oxygen and nitrogen in petroleum coke calcined at 1350 ℃ is generally less than 0.1%; However, the carbon atoms of sulfur and aromatic hydrocarbons are so firmly combined that the C-S bond begins to break at more than 1400 ℃ to form sulfur and sulfur carbon compounds; At higher temperatures, mainly at 1500-1800 ℃, the generated sulfur and sulfur carbon compounds are rapidly released from the products in the form of gas, which produces great internal stress on the products and forms small holes and cracks in the products. When the sulfur content reaches a certain degree, it often leads to cracks in the products during graphitization, contact us to read more technical news.
No related results found
0 Replies