Current status of domestic anode baking furnaces
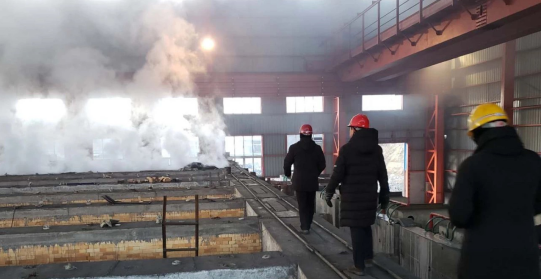
A new type of horizontal wall bricks used in open baking furnaces
The progresses in the baking process of prebaked anode have been made in our country since the introduction and application of the technology in combustion device of anode baking furnace. To get the high quality graphite electrode used in baking furnace. But the lengthened life cycle of anode baking furnace comes along with air leakage of the chamber, which causes the increasing of gas cost, and affects the product quality. Considering of above problems, a new type of horizontal wall bricks used in baking chamber has been developed. By using the new technique, both the air leakage and increasing gas cost are solved successfully, and the homogeneity stability of carbon anode is increased greatly.
1. Current status of domestic anode baking furnaces
The anode baking furnace is the most important energy-consuming equipment in the field of carbon for aluminum. With the country's promotion and implementation of energy saving and emission reduction policies, the domestic anode baking furnace energy-saving technology has been rapidly developed, and the unit energy consumption of anode baking has also been greatly reduced. However, there is still a certain gap compared with the advanced level of foreign countries.
In recent years, the energy-saving work of aluminum pre-baked anode baking furnaces has received great attention in the carbon industry. With the application of various energy-saving technologies, the energy consumption of domestic anode baking furnaces has shown a downward trend, but compared with foreign countries, there is still a certain gap. Table 1 is the comparison of energy consumption indicators of anode baking furnaces at home and abroad.
The main structure of the aluminum pre-baked anode baking furnace is to use the fire channel wall and the horizontal wall to form a baking box, and the green anode and filler are loaded into the box. Under the condition of isolation from the air, the raw anode products in the material box are indirectly heated by the high-temperature flue gas in the fire channel. The heating cycle is generally 168~216 hours, and a furnace chamber is moved every 28~32 hours. The baked product completes the whole baking process after preheating, heating, constant temperature, and cooling, etc. It is characterized by periodic operation, continuous operation, large capacity, stable product quality, high degree of automation, and high fuel utilization.
2. Anode baking furnace control
Baking and combustion operations and management are mainly to control and adjust the temperature and negative pressure of the furnace chamber in different time periods and at different positions according to the baking curve. During the whole baking process, the control quantity is affected by many factors: such as the size of the negative pressure, the oxygen content in the fire channel and the air flow rate, the degree of sealing of the furnace body, the amount of fuel injection, etc. The sealing degree of the baking furnace has the greatest influence on the energy consumption of the baking furnace..
2.1 Baking furnace combustion control
One of the keys to the control of baking and combustion is to control the fuel supply. According to each fire channel, the temperature situation at each moment is different, and the fuel supply is regulated. When the temperature rise rate is small or is close to the set value, the fuel supply is small; when the temperature rise rate needs to be increased or the temperature is low, the fuel supply is increased. Volatile is an important fuel source. Controlling the volatile to burn in the middle of the anode preheating stage is very beneficial to reduce the energy consumption of baking.
Another key to controlling optimal combustion is the supply of air volume with oxygen. The oxygen required for a certain amount of natural gas combustion is fixed. Excessive combustion supporting air is not only useless, but also lowers the combustion temperature, takes away heat, and causes a waste of natural gas. Small air volume will cause the fire channel hypoxia, natural gas and volatiles can not be fully burned, a waste of natural gas and volatiles, and the flue gas surplus combustible components, there is a risk of explosion. On the contrary, the air volume is large, the oxygen excess coefficient is large, and a large amount of excess air will take away the heat in the preheating furnace chamber and reduce the flue gas temperature, the volatiles cannot be fully burned, and a large amount of volatiles is taken away, resulting in an increase in the energy consumption of baking.
2.2 Control of the negative pressure of the baking furnace
The control of negative pressure in the baking furnace control process is also very important. If there is no reasonable negative pressure control, it will not be possible to control the volatilization rate during the anode baking process and its full combustion.
For the baking system, the temperature and negative pressure adjustment is a mutually restrictive process. The large negative pressure can ensure full combustion of the gas, but because the large negative pressure takes away more heat, the preheating zone heats up quickly, which does not meet the heating requirements. If the negative pressure is too small, the intake of hot air is too little, the fuel combustion is not complete, the temperature of the furnace chamber in the baking zone will not rise, and the gas will easily flow forward, destroying the heating system. Therefore, the principle of the negative pressure adjustment of the furnace chamber is: under the premise of meeting the heating curve, the negative pressure should be adjusted to the minimum.
2.3 Measures to reduce the energy consumption of anode baking
From the perspective of the total heat balance of the baking furnace, the heat income items mainly include the combustion of fuel, the combustion of pitch volatiles, and the combustion of fillers. Reducing fuel consumption is the main way to save energy, and to make the temperature distribution in the fire channel uniform is an effective way to save fuel. Full combustion of volatiles will also correspondingly reduce the proportion of fuel in the heat income. The burning loss of the filler accounts for a small proportion of the heat income (usually about 6%), and it should be reduced from the perspective of reducing production costs.
The heat expenditure items mainly include exhaust smoke loss, heat dissipation loss of the furnace body, heat taken away by the anode and filler, and heat taken by the air cooling the furnace chamber. The exhaust smoke loss is mainly caused by a large amount of air leakage in the fire channel (especially the fire channel in the preheating zone), and a large amount of excess air becomes the main body of the exhaust smoke loss.
Therefore, how to strengthen the sealing of the baking furnace chamber and effectively reduce the air leakage problem of the baking system has become a common concern of domestic pre-baked anode manufacturers for more news contact us.
No related results found
0 Replies