Improvement measures of the service life of open ring type baking furnace
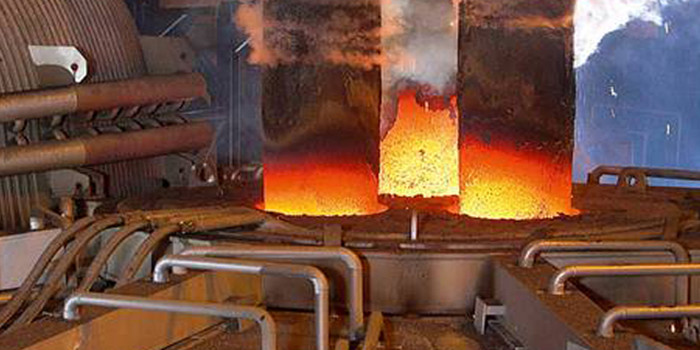
Improvement measures of the service life of open ring type baking furnace
1 Masonry process control of baking furnace
The control of the masonry process of the baking furnace is very important. If the control of the masonry process is not good, it is easy to cause the fire wall of the baking furnace to sink and deform. The traditional process uses refractory bricks and refractory mud for masonry. View information of graphite electrodes for baking furnace. The masonry technology requires horizontal joints and vertical joints without ashing. This will cause the brick joints to fall off and affect the overall structural strength of the fire wall. In addition, the requirements for vertical and horizontal joints are too large, and the volume of the refractory mortar shrinks after baking and reburning at high temperature, causing the fire wall to sink as a whole.
Improvement measures:
When building the baking furnace, the company revised the technical requirements for vertical and horizontal joints, and revised the original requirement (2±0.5) mm to (1.5±0.5) mm, and required that the mortar is full and the masonry process is well controlled in a certain area on the whole fire path wall.
It is very important to reserve expansion joints at both ends of the fire wall, horizontal wall and end wall of the baking furnace. The design size of the expansion joint is designed according to the change of the refractory line and the thermal expansion rate of the refractory brick. If the expansion joints on both sides are reserved too small, there is no expansion margin after thermal expansion of refractory materials, the fire wall and horizontal wall are prone to distortion and deformation. The company revised the original baking furnace masonry technical requirements on the basis of the original design and combined with the on-site process, as shown in Table 3.
2 Oven process
If the baking process is not well controlled, it is easy to cause the baking furnace to sink and deform. For the aluminum carbon industry, the start-up of the anode baking furnace is an important task. Whether it is the commissioning of a new baking furnace,or the technical transformation of the original furnace or the large-scale restoration of production, the furnace needs to be started. The purpose of the oven is to dry the moisture contained in the furnace body, and also to make the mortar joints of the furnace wall reach a better strength, improve the high temperature resistance of the furnace wall, and form a solid whole. If the oven process is not well controlled, and the fire wall has not reached a certain degree of dryness, the oven wall will crack, sink, and deform due to the uneven expansion of the oven wall after being heated rapidly.
Improvement measures:
After the completion of the basic construction of the baking furnace, there was no rush to carry out the furnace operation, but a 15-day natural drying period was reserved for the baking furnace just completed. The original "six-chamber baking operation mode" was optimized to the "eight-chamber baking oven mode" for oven operation, and a reasonable heating curve was formulated. The holding period was increased during the low temperature 600~800℃, and the oven process was well controlled. The oven operation has achieved good results.
3 Daily operations
The operation of the ring furnace is that the flame system repeats the cycle according to a certain operating cycle. The flame system moves along the circular route one by one in the furnace chamber, and the furnace numbers contained in it are gradually changing. Each furnace chamber in the flame system goes through the preheating, baking and cooling stages of flue gas in turn. 2 m below the nozzles 1 and 3 where the fuel is supplied on the wall of the fire wall is directly in contact with the fuel, which will easily cause local overheating and depression; relatively speaking, the nozzles 2 and 4 are not easy to cause deformation due to the placement of thermocouple.
Improvement measures:
The operating direction of the flame system is adjusted every two years of operation, from clockwise operation to counterclockwise operation, so that the four nozzles on the fire wall of the baking furnace alternately contact the fuel, which completely solves the problem.
To make improvements in the way of loading and unloading, it is required that the loading and unloading operations must be carried out on a layer-by-layer basis. If the loading and unloading operations are not carried out according to the layer, the filled bin will squeeze the adjacent empty furnace chamber. After the squeezed fire wall is deformed, the size of the material box will change, causing the fire wall to be distorted and deformed, which directly affects the loading. The amount of furnace, resulting in the reduction of baking output.
Manual loading and out of the furnace use the grab hopper to fill the filling material, the collision and extrusion of the grab hopper can also easily cause the deformation of the fire wall, especially if the grab hopper is used to grab the material after the fire channel is deformed, it is easy to squeeze the adjacent furnace out of shape.
The baking process and temperature adjustment operation can also easily cause the fire wall of the baking furnace to dent and deform. If the baking process is not carried out according to the baking process, it is easy to cause the local temperature of the fire wall to be too high. Open the observation hole and you can see the white dazzling phenomenon in the local wall of the fire path, if the negative pressure is too large at this time, it will cause partial depression of the fire wall and sinking of the middle part of the fire channel in a short time, and the fire channel will be distorted and deformed in severe cases.
It is very important to strengthen the maintenance during the use of the baking furnace. The curved wall of the baking furnace is not formed temporarily, but the distortion is increasing due to long-term non-maintenance, and finally it has to be demolished and rebuilt. In order to extend the service life of the baking furnace, the company has developed a fire wall straightening machine since 2007. After each flame cycle, the straightening machine is used to correct the slightly deformed fire wall, and the effect is more obvious.
4 Conclusions
(1) Through continuous improvement of baking furnace design, infrastructure construction, and subsequent maintenance, the service life of the baking furnace has been extended. The furnace body of the baking furnace that has been in operation for 10 years is in good condition and has reached the international advanced level through identification.
(2) Strictly control the various physical and chemical indexes of refractory materials for baking furnaces. All materials shall be spot-checked and inspected from time to time to ensure that the refractory materials used meet the technical requirements.
(3) Carry out masonry in strict accordance with technical requirements, strengthen the process management of baking furnace masonry, and strictly control the gaps between each layer of refractory bricks during masonry. Rework must be carried out if they fail to meet the standards.
(4) Strengthen the operation management of the oven, formulate a reasonable heating curve and heating plan for the oven. Standardize the operation of loading and unloading and temperature adjustment, and continue to optimize the baking process.
(5) Strengthen the daily maintenance work in the later stage of the baking furnace, get super high quality graphite electrodes for baking furnace. and use the straightening machine to straighten the slightly deformed fire wall in time.
No related results found
0 Replies