Three-phase multi-electrode layout submerged arc furnace power transmission and smelting
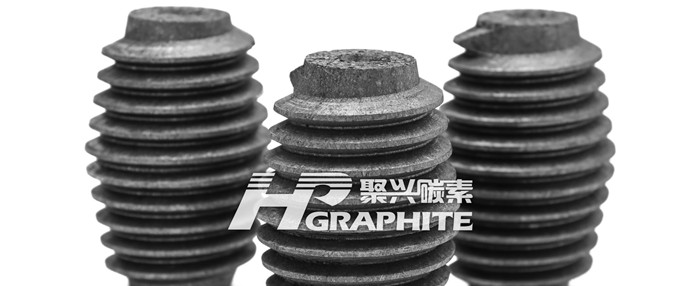
1 The layout of three-phase multiple extruded graphite electrodes in submerged arc furnace
The smelting steps of CHP electrode in submerged arc furnace:
1) Each phase of the three-phase terminal on the secondary side of the transformer is divided into at least two parallel electrode terminals, and each electrode terminal is connected with a column electrode respectively; Or, the three-phase terminal of the secondary side of the transformer is divided into at least two groups of the same polarity, and each group is connected with a column electrode respectively;
2) According to the capacity of the furnace, the diameter and number of high quality extruded graphite electrodes were selected, and the electrodes were inserted into the furnace from the top of the furnace cover of the furnace. In addition, the adjacent electrodes were of different phases, and the three electrodes of different phases were evenly distributed in an equilateral triangle.;
3) The three-phase multi-electrodes are distributed evenly and reasonably in the furnace for power transmission and work, and the high-temperature melting zone and the reduction reaction production zone in the furnace are enlarged, and the coverage areas overlap each other, which greatly saves power and electrode consumption.
The power supply layout of the three-phase 6 or 9 or 12 GHP electrodes of the AC ore furnace is shown in Figure 1.
At present, the maximum diameter of vibrating formed carbon electrode and graphite electrode is Φ1400 mm. According to the habitual thinking, the submerged arc furnace continues to increase the transformer capacity and it is necessary to design the use of larger diameter electrodes. In order to ensure the quality of large-diameter products, the investment in process and technical equipment will be huge, and it is unknown whether the level of process and equipment can meet the ideal requirements, and the manufacturing cost will be far greater than that of GHP graphite electrodes. The application of three-phase 6 or 9 or 12 Φ600~800 mm high quality graphite electrode layout submerged arc furnace power transmission smelting new technology method can meet the development requirements of larger capacity submerged arc furnace, and can achieve over 40 000 kVA high-capacity submerged arc furnace production, and can also be designed to allow high-power and high-current to rapidly strengthen smelting production in a large range, expand the high-temperature melting zone at the bottom of the electric furnace, and improve smelting efficiency.
The corresponding relationship between the different submerged arc furnace capacity and the diameter of the conductive electrode is shown in Table 2.
2 The energy-saving effect of applying new technology smelting methods
(1) Effectively reduce unit consumption and save power
The application of three-phase 6 or 9 or 12 Φ600~800 mm extruded graphite electrodes layout large-capacity submerged arc furnace smelting will reduce the unit consumption by about 80% and the energy consumption by about 40% compared with the Self-baking electrode; compared with the carbon electrode unit consumption, the unit consumption is reduced by about 50%, and the energy consumption is reduced by about 20%; compared with the large-scale vibration forming graphite electrode for the large-capacity submerged arc furnace, the comprehensive energy consumption will be reduced by more than 10%. Table 3 shows the comparison of unit consumption and power consumption of different electrode power supply modes for submerged arc furnaces such as calcium carbide and ferroalloy.
(2) Apply new technology smelting methods to reduce carbon emission
After the application of new technology smelting methods, due to the substantial reduction in comprehensive energy consumption, CO2 emissions will be greatly reduced. Especially for calcium carbide and ferroalloy smelting enterprises using self-baking electrodes, if they can quickly apply new smelting technology and methods, CO2 emissions will be greatly reduced.
For example, the actual production capacity of the calcium carbide industry in 2015 was 25 million tons, and 700,000 tons of electrode paste was needed, which could be replaced by 100,000 tons of GHP products.
For example, the actual production capacity of the ferroalloy industry in 2015 was 30 million tons, and 600,000 tons of electrode paste were needed, which could be replaced by 100,000 tons of GHP products.
These two industries alone will reduce carbon emissions by more than 1 million tons to view more technical information contact us.
No related results found
0 Replies