Measures for carburization behavior of low-carbon steel during smelting process
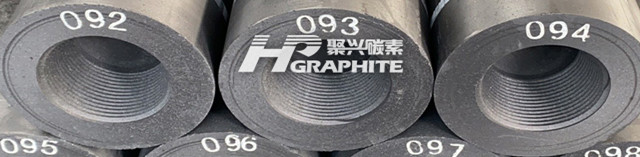
1 Measures taken to increase the carbon of low-carbon steel
Apply the bottom-level event analysis results, combined with the controllable status and difficulty of the smelting process, and take measures as follows:
(1) Adjust the inclination angle of the conductive arms so that the three-phase inclination angle of electrode ABC is the same, to view graphite electrodes information here, and the reactance is balanced (Table 6).
(2) Adjust the angle of the bottom blowing argon gas hole from 75° to 150°, as shown in Figure 3.
The double-hole axisymmetric bottom-blowing method (Figure 3(a)) and the double-hole center-symmetric bottom-blowing method Figure 3(c) have their own advantages and disadvantages in the application of refining ladle furnaces. The advantages of the double-hole axisymmetric bottom blowing method are that the molten steel has a fast surface flow rate, a relatively short mixing time, and fast removal of inclusions. However, due to the different viscosity coefficients of the molten steel at different temperatures, the bottom blowing argon gas flow is not easy to control. The advantage of the double-hole center symmetric bottom blowing method is that the surface flow speed of molten steel is relatively slow, and the mixing time and argon gas flow rate are relatively easy to control. Combining the advantages of the double-hole axial symmetry and the double-hole center-symmetric bottom blowing method, the original bottom blowing angle of 75° is changed to a bottom blowing angle of 150°, as shown in Figure 3(b).
(4) Adjust the graphite electrode formula according to the needs of low-carbon steel smelting. Mainly adjust the ratio of large and medium particles, improve the thermal shock resistance of the graphite electrode at high temperature, and reduce the cracking of the electrode. At the same time, high temperature glue is used to brush the joints to make the threads adhere to each other tightly to prevent falling off.(3) Adjust the supply of argon gas. The supply of argon gas is adjusted from 50~100m3/h to 20~40m3/h, which slows down the flow rate of molten steel and the erosion of foam slag on the electrode, and at the same time overcomes the phenomenon of slag entrapment and optimize the mixing time.
See Table 7 for the comparison table of graphite electrode formulations improved for low-carbon steel production.
2 Implementation effect
After the implementation of the above measures, significant results have been achieved. The number of furnaces for low-carbon steel exceeding the standard has been greatly reduced, the electrode consumption and power consumption have been reduced, and the smelting time has been relatively shortened (see Table 8). After improving the argon gas bottom blowing hole and the argon gas bottom blowing flow rate, the dead zone area of the molten steel is greatly reduced, and the mixing degree of the molten steel is improved. At the same time, the phenomenon of the graphite electrode hole wall falling off and the arc at the bottom of the electrode are also improved (see Figure 4). By adopting the above measures, the electrode cost is saved by 120,000 yuan and the electricity cost is saved by 250,000 yuan.
3 Conclusion
Applying the fault tree analysis method to analyze the carbon increase behavior of low-carbon steel can draw the following conclusions:
(1) The carbon increase behavior of low-carbon steel is not only related to the electrode, but also closely related to the control of the smelting process. To reduce the carbon increase of the graphite electrode, every step of the smelting equipment must be carefully overhauled during the major and medium repair of the electric furnace, in order to optimize the operation of the electric furnace and reduce the phenomenon of carbon increase.
(2) The carbon from the converter, the bottom blowing angle and the bottom blowing rate are also very important for the control of the carbon increase of low-carbon steel. The high carbon coming from the converter, the small bottom blowing angle of argon gas, and the large bottom blowing flow will all affect the carbon increase behavior of the graphite electrode on molten steel.
(3) The carbon increase of low-carbon steel by graphite electrodes is mainly due to the arcing at the lower end of the electric furnace at high temperature, the carbon in the electrode enters the foam slag and reacts with the metal oxides in the slag liquid to form carbides and enter the molten steel to directly increase the carbon.
(4) At present, various carbon manufacturers do not have graphite electrodes exclusively for low-carbon steel smelting. The development of graphite electrodes for low-carbon steel smelting is also a direction to reduce the carbon increase of low-carbon steel, contact us for more technical knowledges.
No related results found
0 Replies