Judgement for the shutdown of Acheson graphitization furnace
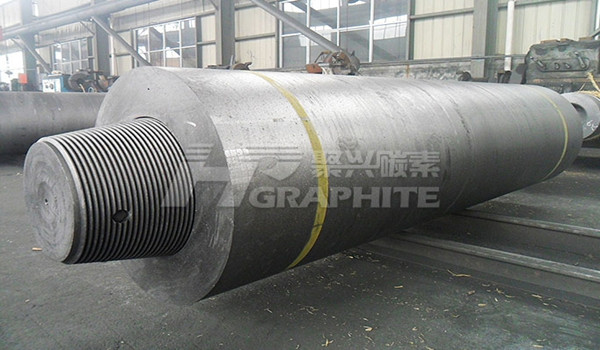
At the present situation of graphite electrode production in the graphitization process, power distribution system was used to control the rising rate of furnace core temperature of Acheson graphite furnace, and cumulative amount of power to achieve the final plan power outage was the basis of the shutdown of Acheson graphite furnace, which has many defects. The ideal shutdown method is given according to the later stage furnace resistance changes of graphitization. To accurately determine the best time to stop the graphitization furnace was from the duration of minimum furnace resistance and power consumption. Under the premise of ensuring the quality of products, it can save electricity consumption and reduce production costs.
The Acheson graphitization furnace is the main type of furnace for producing carbon products. The graphitization process uses the resistance of the furnace core to convert electrical energy into heat under the action of a strong current, so that the product reaches the highest temperature required for graphitization to complete the graphitization process. During the whole graphitization process, as the temperature of the furnace core increases, the resistance of the furnace core generally shows a decreasing characteristic. When the furnace core resistance drops to a minimum and keeps it for a period of time, as the furnace core temperature continues to rise, the furnace core resistance rises. The traditional shutdown method of Acheson Graphitization is based on the power outage due to the accumulated power finally reaching the planned power. This method has many shortcomings and is extremely unscientific. According to the actual production of the Acheson graphitization furnace, this article briefly summarizes and analyzes the optimal shutdown judgment method, in order to ensure the quality of graphite products without wasting electric energy.
1 Overview of Acheson graphitization
1.1 Graphitization mechanism
In the process of graphitization, the arrangement of carbon atoms changes from a two-dimensional disordered state (amorphous carbon) to a three-dimensional ordered state (graphite crystal structure), that is, a physical structural change dominated by crystal growth and an increase in the orderly overlap of the inner layer of the crystal, the higher the heat treatment temperature, the smaller the crystal interlayer spacing, which is closer to the ideal graphite crystal interlayer spacing of 0.335 nm.
1.2 The 3 temperature stages of the graphitization process
① Room temperature to 1300℃ is the repeated roasting stage, and the product will not crack when using a faster heating rate;
② 1 300~1 800℃ is the strictly controlled heating stage, the carbon plane grid is gradually transformed into a graphite lattice structure. If the internal temperature gradient of the product is too large, it is easy to cause cracks. Therefore, the effect of thermal stress should be slowed down to keep the product in a smaller temperature gradient;
③ 1 800℃ to the highest graphitization temperature is the free heating stage. At this time, the graphite crystal structure of the product has basically formed, and the heating rate has little effect on the product. At this time, the enhanced graphitization power transmission system can be adopted to increase the furnace’s current density of the core, in the shortest time, makes the power reach the highest, the current reaches the maximum rated current, so that the furnace core temperature can reach the highest temperature required for the perfect graphitization process of the product as soon as possible.
1.3 Composition of furnace core resistance
The core resistance of the Acheson graphitization furnace is mainly composed of the resistance material and the baked product loaded into the furnace. The resistance of the resistor material accounts for 99% of the furnace core resistance at the initial stage of power-on, and it accounts for about 97% after the power-on. Therefore, the resistive material plays a dual role of energized heating and heat transfer during the entire graphitization process. The commonly used resistance material is a mixture of metallurgical coke and graphitized coke in a certain proportion. The resistance of the graphitization furnace is mainly determined by the following factors:
① The resistivity of the resistive material itself;
② The resistivity of the baked product;
③ The contact resistance between the coke particles of the resistive material;
④ The contact resistance between the resistive material and the baked product.
1.4 The change of furnace resistance in each heating stage
The change of furnace resistance at each heating stage is shown in Figure 1. The heating stages are described as follows:
① From room temperature to 1 300 °C (power supply for 0-20 h), the volume of the baked product and the resistor material expands sharply at this stage, the resistance of the resistor material is greatly reduced, the pressure between the resistor material particles increases, and the contact resistance of the resistor material is greatly reduced , so the entire furnace resistance drops quickly.
② Strictly control the temperature rise stage at 1 300~1 800 °C (power supply for 20~45 h). In order to prevent the stress concentration caused by air expansion and lead to cracks, the curve is usually slowed down. In the early stage, the products in the furnace shrink, the contact resistance increases with the decrease of the pressure, and the furnace resistance decreases slowly. As the furnace temperature continues to rise, elements such as nitrogen and sulfur in the thermal expansion lattice of the baked product escape, resulting in increased expansion, reduced contact resistance, and a faster decline in furnace resistance.
③ From 1 800 °C to the highest graphitization temperature (power supply for 45 hours and above), due to the rapid increase of power and current, the temperature of the furnace core increases rapidly, the baked product expands again, and the contact resistance of the resistive material decreases, so the furnace resistance continues to decrease. In the constant power stage, due to the further growth of graphite crystals, the baked product shrinks to varying degrees, and the resistance of the baked product further decreases, but the contact resistance increases due to the decrease in pressure, and the furnace core resistance tends to stabilize, and even a certain rise talk with us to get more technical guidance.
No related results found
0 Replies