Development of new type baking furnace horizontal wall bricks
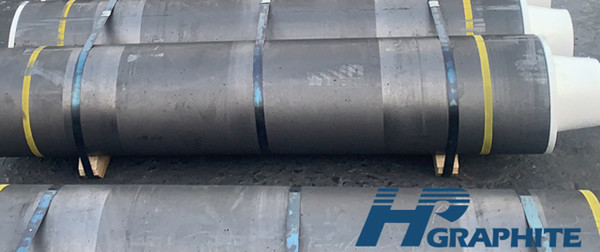
Development of new type baking furnace horizontal wall bricks
The top brick of the traditional fired horizontal wall is built with 400 mm thick prefabricated blocks. There is no smoke exhaust hole on the top of the horizontal wall. The smoke exhaust hole is on the fire channel wall. The prefabricated block on the top of the fire channel wall has 4 holes. Get the baking furnace used graphite electrode. These holes are used for cooling, blowing, burning, temperature measurement and insertion of negative pressure baffle, etc. The traditional negative pressure baffle adopts a folding insert plate, which is inserted through the peephole of the fire channel to block the air flow. However, with the increase of the operating cycle of the baking furnace, the fire channel wall will be deformed, and the fire channel insert plate is not tightly sealed, and the air leaks. A large amount of gas escapes from the upper part of the baffle in the horizontal direction, taking away a large amount of heat and reducing the temperature of the anode, flue and flue gas, which not only increases fuel consumption, but also breaks the balance of negative pressure in the combustion zone, which seriously affects the temperature distribution in the material box and the furnace chamber, which will affect the quality of the anode and is not conducive to the uniformity and stability of anode quality.
In order to solve the sealing problem of the baking furnace, Yidian Holding Group Co., Ltd. successfully developed a new set of horizontal wall bricks for the baking furnace. The brick has the characteristics of low thermal conductivity, high refractory temperature, high compressive strength and easy operation. It is used in the baking furnace to change the position of the negative pressure plate of the traditional fire channel, improve the sealing performance of the fire channel, reduce the air leakage in the baking preheating zone, optimize the negative pressure of the baking system, increase the utilization rate of volatiles, reduce the unit consumption of natural gas, and archive energy saving and consumption reduction of baking furnace. Figure 1 shows the comparison before and after renovation of the horizontal wall of the baking furnace.
Application of new type baking furnace horizontal wall bricks in anode baking furnace
1. Improve the sealing performance of the baking furnace surface
After the new type of baking horizontal wall bricks were put into use in the company's baking workshop, the sealing performance of the furnace surface was significantly improved, and the air leakage of the system was effectively controlled.
2. Optimize the negative pressure of the fire channel and improve the volatile utilization rate
After the application of the new horizontal wall bricks of the baking furnace, the sealing performance of the baking furnace surface can be improved. The negative pressure of the fire channel branch pipe is increased from 60~80 Pa to 80~100 Pa, with an average increase of 20~30 Pa, which fundamentally solves the problem of insufficient negative pressure in the baking system.
With the increase of the negative pressure on the furnace surface, optimize the negative pressure balance point of the fire channel in the daily operation process, reduce the air leakage of the system, realize the reasonable supply of combustion air, reduce the excess air coefficient, reduce flue gas emissions, and reduce the baking heat loss, achieve the full combustion of volatiles in the fire channel and reduce the emission of baking pollutants. From Figure 2, it can be seen that there is no combustible material attached to the flue after the renovation. The change in the residual oxygen content of the flue gas before and after the renovation is shown in Figure 3.
3. Optimize the baking temperature rise curve
After the promotion and application of the new type of baking furnace horizontal wall bricks, according to the operation of the baking system, the company's baking temperature rise curve was optimized and adjusted, as shown in Table 2. The baking curve is adjusted from the original 192 h to 180 h, and the baking time is reduced by 12 h. At the same time, increase the starting temperature of the heating zone, gradually increase the starting temperature of the heating zone from 900 °C to 920 °C, reduce the heating rate of 4P and 5P, and reduce the heating rate from 8 °C/h to 6 °C/h, effectively improving heat transfer efficiency, avoid heating peaks, reduce the frequency of natural gas combustion, ensure sufficient natural gas combustion, and achieve the purpose of saving gas.
4. Reduce the unit consumption of natural gas and improve the quality of anodes
With the improvement of the sealing performance of the baking system and the optimization of process control, the utilization rate of volatiles has been significantly improved, and the temperature distribution of the baking furnace workbin is more uniform. Not only the unit consumption of natural gas is reduced, but the anode mass uniform stability has also been improved, the anode first-class product rate has reached over 85%, and the anode CO2 reaction residual rate has reached 89%.
The unit consumption of anode natural gas has been reduced from 60.86 m3/t before the renovation to 56.39 m3/t after the renovation.
Conclusion
(1) The uniformity of temperature distribution in the fire channel, the full combustion of volatiles, the amount of air leakage in the fire channel, the degree of solid heat storage recovery (air preheating) and the heat dissipation of the furnace are the main factors that affect the energy consumption of the baking furnace.
(2) The application of the horizontal wall bricks of the new type of baking furnace successfully solved the problems of the deformation of the fire channel wall, the lax sealing of the fire channel and the serious air leakage due to the increase of the age of the baking furnace. It can effectively increase the negative pressure of the fire channel, optimize the operation of the baking furnace, increase the utilization rate of volatiles, reduce the time of furnace transfer, simplify the difficulty of furnace transfer, reduce labor intensity of employees, reduce natural gas consumption, reduce baking flue gas emissions, and reduce pollutants emissions.
(3) After the completion of the renovation, the unit consumption of natural gas has been reduced by 4.47 m3/t, and the annual production of 300,000 tons of pre-baked anode production enterprises can save 1.341 million m3 of natural gas and save about 3.8 million yuan in capital.
(4) After the completion of the renovation, the sealing performance of the furnace surface has been improved, and the frequency of the fan of the fume extractor has been reduced by 2~3 Hz, which can save 600~700 kW·h per day, can save 220,000 to 250,000 kW·h of electricity annually, and can save about 110,000 yuan for more related news contact us.
No related results found
0 Replies