Affecting reasons of the service life of open ring type baking furnace
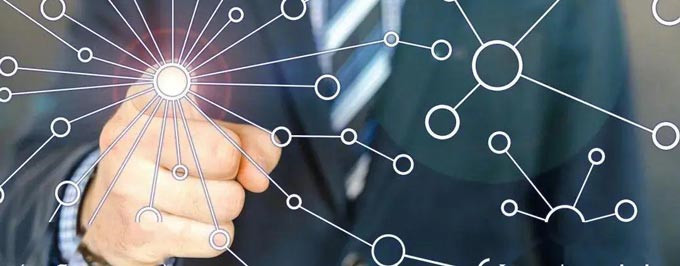
Affecting reasons of the service life of open ring type baking furnace
The open ring baking furnace in our country was developed on the basis of digesting the baking technology of Japan Light Metal Company introduced in the early 1980s. After more than 20 years of in-depth research and continuous innovation of baking furnaces by Chinese technicians, the service life of baking furnaces has been improved to a certain extent, but most of the service life is 5~8 years, while foreign baking furnaces generally reach 8~10 years, and some have reached more than 10 years, there is a certain gap in the service life. A company in Shandong has extended the service life of the baking furnace by making a lot of improvements in the design of the baking furnace structure, the selection of refractory materials and the methods of masonry, and the effect is remarkable. The company's baking furnace was built in 2006 and put into operation in June of the same year. It has been in operation for 10 years now. When the baking furnace was newly built, the fire wall and cross wall were all made of low creep clay bricks and high alumina bricks produced by a refractory factory. There is a baffle wall in the fire tunnel to make the flue gas flow up and down in a W shape in the fire tunnel. There are 4 fire holes on the top of the fire wall to facilitate the operation of fuel supply, temperature and pressure measurement and observation. After the technical improvements made by the company's technicians in the early and new stages of the new baking furnace and the continuous maintenance after it is put into operation, measures to prolong the service life of the baking furnace are proposed to provide guidance and reference for future enterprise production. Table 1 lists the structural performance of baking furnace of the Shandong company. Get HP graphite electrode products.
1 Reasons and improvement measures affecting the service life of the baking furnace
The main reason that affects the service life of the baking furnace is that the fire wall of the baking furnace is recessed, twisted, and deformed. The serious deformation of the fire wall of the baking furnace is bound to affect the quality of the product, especially the output of the baking furnace, thereby increasing the production cost. After the fire wall is recessed and deformed, the size of the material box changes, which cannot meet the production requirements, and the consumption is high, which makes it difficult to obtain better economic benefits. After the company's continuous improvement before the basic construction of the baking furnace, and continuous improvement during the later use, the service life of the baking furnace has been improved.
1.1 The structure and performance indicators of refractory bricks for baking furnace masonry
The performance and physical and chemical indexes of refractory bricks used in baking furnace masonry are one of the key reasons that affect the service life of baking furnace. The low load softening point of refractory bricks is one of the reasons for the sinking of the fire wall. The load softening point of refractory bricks refers to the ability of refractory materials to resist deformation under the simultaneous action of temperature and load. Refractory brick has high compressive strength at room temperature, but it will deform if it is compressed again at high temperature, and its compressive strength will be significantly reduced. The load softening point of refractory bricks does not meet the design standard, or the local temperature exceeds the load softening point temperature, which will directly cause the fire wall of the baking furnace to sink and deform.
As the refractory products for baking furnaces may undergo further sintering and phase changes during use, they will again cause volume changes, resulting in residual shrinkage or expansion after reburning. High temperature volume stability is an important quality index of refractory products. If the refractory brick reburning line used in the fire wall of the baking furnace shrinks too much, it will cause the whole fire wall of the baking furnace to sink. If the expansion amount is too large and is greater than the designed expansion amount, the fire wall is also prone to distortion and deformation. Contact us for more GE technical information.
When the fire wall refractory brick is used for a long time at high temperature, its shape and volume remain stable without change, indicating that its high temperature volume is stable. The high-temperature volume stability will directly affect the service life of the baking furnace. If the high-temperature volume stability is very poor, the baking furnace is prone to a large area of sag within 1 ~ 3 years, and the situation will collapse in serious cases. Therefore, the physical and chemical index of refractory materials is very important during the usage of baking furnace.
The refractory brick structure used in the baking furnace is also one of the main reasons that affect the life of the baking furnace. At present, when designing the baking furnace, many designers only design the bosses and grooves at the upper and lower ends of the refractory brick, as shown in Figure 1(a) show.
In this case, under the re-firing of the high temperature baking, it is easy to cause the gap between the standing seam and the standing seam to be too large, the bonding performance of the fire wall is poor, and it is easy to cause the fire wall to dent and deform, and the product quality is difficult to guarantee.
Improvement measures:
In order to increase the stability of the fire wall of the baking furnace, strengthen the combination of the fire wall, and prolong the service life of the baking furnace. The company put forward technical requirements when designing the baking furnace, and also added grooves and bosses at both ends of the refractory bricks, thereby enhancing the bonding and firmness of the fire wall, and the effect is more obvious, as shown in Figure 1(b) show.
According to the properties and physical and chemical indexes of refractory materials for baking furnaces, the company proposed to use low-creep clay bricks instead of ordinary clay bricks. Low creep clay bricks have low creep rate and strong oxidation resistance at high temperatures. The revised physical and chemical indexes of refractory materials are shown in Table 2. And each batch of refractory bricks arriving at the factory has been spot-checked and tested to ensure that the physical and chemical performance indicators of the refractory materials meet the standards, thereby prolonging the service life of the baking furnace.
1.2 Fireway wall pull brick configuration
The main function of arranging pull bricks in the fire tunnel wall of the baking furnace is to strengthen the firmness and stability of the fire tunnel wall. It is required that it doesn’t affects the flue gas flow during the baking process, but has a uniform temperature distribution in the fire tunnel. If the pull brick configuration is unreasonable, it is easy to cause a temperature dead angle in the fire channel, and the local temperature difference becomes larger. Moreover, unreasonable or too few pull bricks can easily cause local depression and deformation of the fire wall.
Improvement measures:
The company conducted a joint review of drawings before the basic construction of the baking furnace, and found that the design of the layout of the fire wall was flawed, and the configuration of the upper pull bricks was too few and unreasonable. Immediately revised the original fire wall configuration drawing and added the pull brick configuration. After use, it was found that the local depression and deformation problem was solved, the flame distribution was more uniform, and the product quality was stable. The comparison before and after the transformation is shown in Figure 2.
No related results found
0 Replies