Technology|Graphite products graphitization crack reason analysis Ⅱ
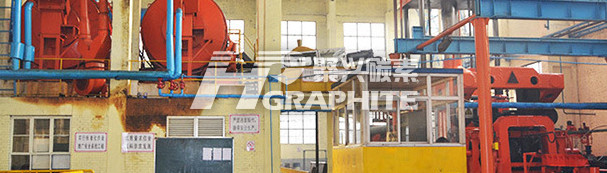
Technology|Graphite products graphitization crack reason analysis Ⅱ
4. Product graphitization crack prevention
a. Graphitization process should be reasonable
Selection of furnace loading method
In the production process of Acheson graphitization furnace, reasonable charging mode is the guarantee of product graphitization. To view the good quailty graphite electrodes. Whether the products are installed vertically or horizontally, whether the products should be installed vertically or horizontally, whether they should be installed incorrectly or not, should be determined according to the product variety, specifications, quality standards and technological parameters of the equipment, so as to ensure that the products are heated relatively evenly in the furnace core, reduce the thermal stress and reduce the cracks of the products in the graphitization process. For the products of large size, the 1/2D furnace loading method of dislocation can reduce the crack of the products, and have good graphitization effect. For products with high scrap rate and unstable quality of graphitized crack, the measure of core flow equalization can also be adopted.
Determine a reasonable power system
The temperature of the graphitized furnace core is controlled by the power curve of constant power distribution. Correctly and reasonably formulating and using the power on system of graphitization furnace is of great significance to improve the yield, save energy and shorten the graphitization cycle of products. The determination of graphitization furnace electrification system should not only take into account the furnace structure, product types and specifications, quality information, resistance material, insulation effect, distribution system parameters and other factors, but also meet the different requirements of the temperature rise speed of the products in different stages of the graphitization furnace.
A reasonable electrification system of graphitized furnace should be a three-stage power curve of "fast--slow--fast", so as to meet the different requirements of the three stages in the temperature rise process of the products. A relatively fast temperature rise of the furnace core should be maintained to reduce heat loss of the graphitized furnace and avoid cracking of products due to the excessive temperature gradient of the furnace core. For products with unstable graphitization quality, it is necessary to strictly control the rising rate of core temperature in the temperature rising stage to avoid cracking of products caused by too fast temperature rising. At this time, the rising power of the power transmission curve should be properly adjusted to form a four-stage power transmission curve of "fast-slow-slow-fast".
Determine the appropriate resistance material
Acheson graphitization furnace is mainly used to heat products through the heat generated by the resistance material. The resistance material is closely related to the change of furnace core temperature. From the perspective of improving the graphitization furnace core temperature, the resistance of the resistance material is required to be larger. Especially in the later stage of power transmission, the secondary output current of the transformer has reached the maximum value. At this time, the furnace core resistance is large, which can maintain high electrical efficiency. However, it is unreasonable that the resistance of the resistance material is too large. Therefore, when determining the resistance material, we should consider not only the equipment performance, but also the product variety, specification and power transmission curve, so that the resistance of the product and the resistance of the resistance material can not be too different. For small and medium-sized products, metallurgical coke can be used as the resistance material, even if the use of higher starting power and faster power rise, products generally will not crack; for large-scale products, it is more appropriate to use mixed coke or graphitized coke as resistance material, so that the resistance of products and resistance material phase difference is smaller, and the temperature difference inside and outside the products is also reduced. Even if the rapid rising power is adopted, the products will not cause cracks.
b. The operation quality shall meet the standards
In the process of graphitization production operation, furnace loading operation is the key. Since the products loaded into the graphitization furnace are not only heating resistance, but also the object to be heated, they are combined with appropriate resistance materials to form the furnace core resistance. Appropriate furnace core resistance is a necessary condition for product graphitization. First of all, the furnace body condition, busbar short_net, power supply system of the equipment is in good condition. During charging, the cross section of the furnace core shall be symmetrical with the conductive cross section to prevent the bias current of the furnace core. The charging operation shall meet the requirements of the process technical regulations. The products shall be arranged horizontally and vertically in the furnace core, the group spacing of the products shall be consistent, and the resistance materials shall be filled well to avoid hanging, so as to ensure that the temperature distribution of the furnace core is balanced during the power transmission of the graphitization furnace. Secondly, the ratio of resistance material should meet the requirements of production technology and technical standards, the quality shall be stable and uniform to avoid the unbalanced temperature distribution of the furnace core in the process of power transmission of graphitization furnace. Thirdly, the graphitization furnace shall transmit power according to the given power transmission curve, and the power fluctuation shall be controlled within the normal range to avoid abnormal fluctuation of power transmission power, so as to ensure balanced rise of furnace core temperature.
c. Master the quality information of the previous process
It is necessary to grasp the production situation and quality information of the pre-process in time. According to the production stability and quality technical indicators of the products in the pre-process, and combined with the production practice of the process, formulate feasible graphitization production technology and technical conditions to prevent cracks and waste products in the graphitization process and ensure the stability of graphitization quality. During graphitization charging, the external quality of the products shall be checked one by one. The products that do not meet the technical conditions of graphitization process shall not be put into the graphitization furnace for graphitization, and the materials shall be returned to the previous process in time.
d. Add an appropriate amount of inflation inhibitor into the ingredients
The phenomenon of irreversible expansion and cracking caused by sulfur in graphitization cannot be completely eliminated, but it must be controlled. At present, the more effective way is to control the escape rate of sulfur in the graphitization process of products. The most practical way is to add an appropriate amount of inflation inhibitor when batching, usually 1% - 2% Fe2O3 powder.
As for the mechanism of adding gas expansion inhibitor, it is mainly that the inhibitor can capture sulfur and generate sulfur compounds within the temperature range of graphitization gas expansion of the product, and form gas release in a higher temperature range, so as to broaden the temperature range of sulfur escape, so that the product will not crack due to excessive internal stress caused by the concentration of rapidly escaping gas. The most commonly used inflating inhibitor is Fe2O3 powder. Its action mechanism is that at a high temperature of more than 1000 ℃, Fe2O3 powder is easy to be reduced to form iron or carbon iron compound. The carbon iron compound will further decompose into iron and carbon at a higher temperature. In this process, the formed iron reacts with the sulfur decomposed and released from the product, which is slowly released in the form of iron sulfide, so as to slow down the escape rate of sulfur content in the product, play a role in inhibiting sulfur. The relevant chemical equation is:
Because Fe2O3 powder not only has high chemical affinity for sulfur in products and good sulfur inhibition effect, but also has abundant resources and low price, it will not have any adverse effect in the process of electric furnace steelmaking. In addition, Fe2O3 powder also has strong catalytic effect on the graphitization process of products and is an excellent graphitization catalyst. It can be seen that for petroleum coke with high sulfur content, adding an appropriate amount of Fe2O3 powder, an inhibitor of air expansion, can play a role in the production of carbon-graphite products.
Conclusion
In short, the causes of crack waste products produced during graphitization heat treatment of carbon graphite products are various and complex. To prevent crack waste products produced during graphitization heat treatment of carbon graphite products, it is necessary to take various process and technical improvement measures and pay equal attention to samples. The most important thing is that the body quality of the products should be high, the heat resistance should be good, and the homogenization production should be achieved. The quality and technical indicators of the previous process shall meet the requirements of the production process and technical standards, and the quality fluctuation shall be controlled within the normal range. In addition, during the graphitization heat treatment process, the temperature rise speed of the products in the core of Acheson graphitization furnace shall be strictly controlled to avoid the rapid rise of the core temperature and the increase of the internal temperature difference of the products, resulting in the corresponding increase of thermal stress and crack waste products, to read more technical news contact us.
No related results found
0 Replies