Advantages & disadvantages of graphite purification Methods
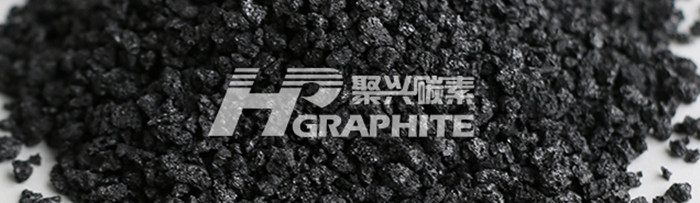
Advantages & disadvantages of graphite purification Methods
With the continuous development of science and technology, graphite is widely used in semiconductor, photovoltaic power generation, environmental protection, chemical industry, military, aerospace and other fields with its unique structural characteristics, conductivity, thermal conductivity, lubricity, high temperature resistance and chemical stability. Get high quality graphite powder detail information. As a necessary non-metallic material for the development of modern industry and high technology, it plays a more and more important role in economic development.
China's natural graphite has superior geological conditions, wide distribution, rich resources and good quality. Its reserves and output rank first in the world. It is one of the main minerals in China. Natural graphite can be divided into crystalline graphite and invisible graphite according to its crystallinity. The carbon content of crystalline graphite ore in nature is generally no more than 10%, the content of invisible graphite is high, and the fixed carbon content is generally 60% - 80%, up to 95%, but the ore washability is poor.
Graphite contains impurities, mainly potassium, sodium, magnesium, calcium, aluminum silicate minerals. The purification process of graphite is to take effective measures to remove these impurities. At present, the methods of purifying graphite mainly include flotation method, alkaline acid method, hydrofluoric acid method, chlorination roasting method, high temperature method and so on.
01 Flotation method
As the surface of graphite is not easily infiltrated by water, it has good floatability and is easy to separate it from impurity minerals. The flotation of graphite ore generally uses the direct flotation method first, and then reverse flotation of the direct flotation concentrate. High grade graphite concentrate can be obtained by flotation. The grade of flotation graphite concentrate can usually reach 80% ~ 90%, and the purity can reach about 98% by multi-stage grinding.
The grade of graphite concentrate purified by flotation method can only reach a certain range. Because some impurities are very fine-grained and disseminated in graphite flakes, even fine grinding can not completely dissociate monomers, it is difficult to completely remove these impurities by physical beneficiation method. Generally, it is only the first step of graphite purification. The methods for further purification of graphite usually include chemical method or high-temperature method.
02 Alkaline acid method
The principle of purifying graphite by alkaline acid method is to mix NaOH and graphite evenly and calcine them according to a certain proportion. At a high temperature of 500 ~ 700 ℃, impurities in graphite such as silicate, aluminosilicate and quartz react with sodium hydroxide to produce soluble sodium silicate or acid soluble sodium aluminosilicate, and then wash them with water to remove them to achieve the purpose of desilication; Another part of impurities, such as metal oxides, remain in graphite after alkaline melting. The products after desilication are leached with acid to convert the metal oxides into soluble metal compounds. Impurities such as carbonate in graphite and acid soluble compounds formed during alkaline leaching react with acid and enter the liquid phase, and then separate from graphite through filtration and washing. Graphite is chemically inert and stable. It is insoluble in organic and inorganic solvents and does not react with alkaline ; Except strong oxidizing acids such as nitric acid and concentrated sulfuric acid, it does not react with many acids, especially hydrofluoric acid; It does not react with water and steam below 6000℃. Therefore, graphite properties remain unchanged during purification.
03 Hydrofluoric acid method
During hydrofluoric acid purification, graphite and a certain proportion of hydrofluoric acid are added to the reactor with stirrer after preheating. After being fully moistened, the stirring is timed. The reactor temperature is controlled by the thermostat. After reaching the specified time, the excess acid is removed in time. The filtrate is recycled. The filter cake is washed to neutral by hot water, dehydrated and dried to obtain the product.
Hydrofluoric acid method is a better purification program, has been industrialized production in the 1990s, Europe and The United States and other countries than our country more common use. Because this method is highly corrosive and toxic to equipment, dilute acid and fluoride were used to remove impurities in graphite more than ten years ago. Japanese and French patents have introduced the reaction of ammonium hydrogen fluoride or ammonium fluoride with graphite powder with carbon content of 93%, which can increase the fixed carbon content of graphite to 99.95%. Due to the high toxicity of hydrofluoric acid, the production process must have strict safety protection and wastewater treatment systems.
04 Chlorine roasting
Chlorination roasting method is to add a certain amount of reducing agent to graphite powder, roast it at a certain temperature and specific atmosphere, and then add chlorine for chemical reaction to make the valuable metal in the material change into chloride and complex of gas phase or condensed phase with low melting boiling point, so as to separate it from its other components and achieve the purpose of purifying graphite.
The impurities in graphite can be decomposed into simple oxides, such as SiO2, Al2O3, Fe2O3, CaO, MgO, etc., under the action of reducing agent after heating at high temperature. The melting boiling point of these oxides is high, while the melting boiling point of their chlorides or metal complexes formed with other trivalent metal chlorides (such as cafecl4, naalcl4, kmgcl3, etc.) is low, The vaporization and escape of these chlorides improves the purity of graphite. The metal complex discharged in gaseous state will soon become a condensed phase due to the decrease of temperature. This characteristic can be used for the treatment of escaping waste gas.
Chlorination roasting method has the advantages of energy saving, high purification efficiency (> 98%) and high recovery. The toxicity, severe corrosiveness and environmental pollution of chlorine gas limit the popularization and application of chlorination roasting to a certain extent. Of course, it is difficult to produce ultimate purity graphite by this process, and the process system is not stable enough, which also affects the application of chlorination method in actual production. This method needs to be further improved and improved.
05 High temperature purification
Graphite is one of the substances with the highest melting and boiling points in nature, with a melting point of 3850±50℃ and a boiling point of 4500℃, while the boiling point of silicate minerals are in 2750℃ (quartz boiling point) below. The boiling point of graphite is much higher than that of the impurity silicate. This characteristic is the theoretical basis of graphite purification by high temperature method.
Put the graphite powder directly into the graphite crucible and heat it to 2300 ~ 3000℃ in the purification furnace filled with inert gas and Freon shielding gas for a period of time, and the impurities in the graphite will overflow, so as to realize the purification of graphite. High temperature method generally uses high carbon graphite with more than 99% carbon purified by flotation or chemical method as raw material, which can purify graphite to 99.99%. If the process conditions are further improved and the quality of crucible is improved, the purity can reach more than 99.995%.
The high temperature method can produce more than 99.99% of ultra-high purity graphite, but it requires that the fixed carbon of raw materials should be more than 99%, and the equipment is expensive, the investment is huge, the production scale is limited, the electric furnace heating technology is strict, and the air needs to be isolated, otherwise the graphite will begin to be oxidized when it rises to 450℃ in the hot air. The higher the temperature, the greater the loss of graphite. Only special industries with very high requirements for graphite quality (such as national defense, aerospace, etc.) use high temperature method to produce high-purity graphite in small quantities.
Several methods of graphite purification have their own advantages and disadvantages. The alkaline acid method is easy to operate, low production cost and low requirements for production conditions, but the fixed carbon content of graphite is low, which can not reach 99.9% at present. Hydrofluoric acid method has good impurity removal effect and high fixed carbon content, but hydrofluoric acid is highly toxic and corrosive, has strict requirements for safety protection measures and production conditions, and the wastewater is not easy to treat. Chlorination roasting method also needs to be strictly sealed because chlorine is toxic and highly corrosive. High temperature method can produce very high-grade high-purity graphite, which can be used in aerospace, semiconductor and other high-tech fields, but it needs to specially design and build high-temperature furnace, which has high cost, high energy consumption and relatively harsh production conditions, for more technical guidance communicate with us.
No related results found
0 Replies