Comparisons between two baking technologies of graphite electrodes
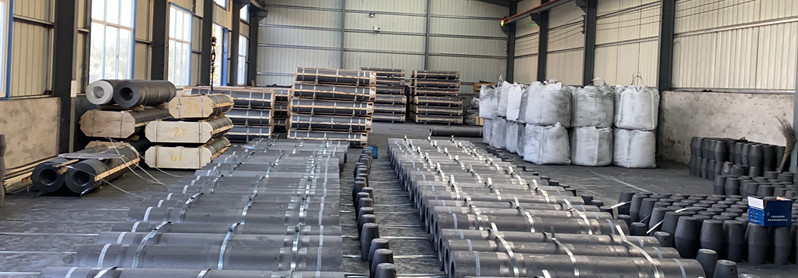
Comparisons between two baking technologies of graphite electrodes
As one of the important heat treatment processes in the production of graphite electrodes, it is a process in which binder bitumen is carbonized to form a whole by firmly coking aggregate and powder particles together. In this process, the raw product undergoes physical changes (the migration of asphalt, the volume expansion and contraction of the product) and complex chemical changes (the decomposition and polycondensation reaction of the asphalt), resulting in different changes in the internal structure of the product, the quality difference in the length direction of roasted products was caused, and the heterogeneity of products was aggravated. The reason is that the temperature fields formed by different firing methods are different, and the raw products are affected by the temperature field effect during heat treatment. The larger the diameter and the longer the length of the raw product, the more serious the impact. The roasting equipment used in the carbon industry includes ring baking furnaces, tunnel kilns, car bottom baking furnaces, inverted flame kilns, rotary bed baking furnaces, single-chamber furnaces and so on. At present, ring baking furnaces and car bottom baking furnaces are used to roast graphite electrodes. This article focuses on the influence of these two roasting processes on roasting quality.
1 Test conditions
1.1 Ring roaster
18-chamber ring furnace: heating in 6~7 chambers, cooling in 6 chambers, preheating in 2 chambers, other furnace chambers are installed and discharged. There are 5 furnace boxes in each room, and the furnace box dimensions are length 4.5 m ×width 1.05 m × depth 4.9 m.
Filler: 0~6 mm metallurgical coke particles.
Firing curve: 460 h.
Maximum temperature: 1 250 °C.
1.2 Car bottom roaster
Car bottom type baking furnace: length 18.1 m×width 5.65 m×height 6.0 m.
Filling material: The product is packed in a sagger, and the filling material is quartz sand.
Firing curve: 390 h.
Maximum temperature: 850 °C.
1.3 Test products
Φ600 mm×2 900 mm ultra-high power graphite electrode body products and joint products (length 2 000 mm) extruded by a 30 MN hydraulic press.
2 Test data
2.1 Raw products
The same batch of Φ600 mm ultra-high power graphite electrode body extruded 16 pieces (No. 1-8 and 15-22) and joint raw products 12 pieces (No. 9-14 and 23-28) were taken as test samples. The samples are divided into 2 groups. Products numbered 1~14 are loaded into the ring roaster, and products numbered 15~28 are loaded into the car bottom roaster. The bulk density of the raw products is shown in Table 1.
2.2 Roasted products
The roasting and heat treatment of the products adopt ring furnace and car bottom furnace respectively. The first group (No. 1~14) is carried out in a ring furnace, and the second group (No. 15~28) is carried out in a car bottom furnace. After the product is roasted, the roasted product is drilled and sampled, and the sampling positions are respectively at the center of the two ends of the product, and then the physical and chemical indicators of the roasted product are tested in the laboratory. The test data is listed in Table 2.
No related results found
0 Replies